When blasting on a quarry safety is a fundamental criterion for the blast pattern design. However, due to uncertainties that are inherent to the rock mass, the quality of the drilling stage and irregularities in the bench’s free face, it is not possible to guarantee quality without the use of equipment’s that allow for a better understanding of the benches. This is especially true for benches with more than 20 m of height.
With that in mind, a quantitative and qualitative study of the methodology and use of appropriate equipment is necessary to optimize the whole process not only in terms of safety but also for the overall economic aspect with the goal being to obtain the desired granulometry while minimising the formation of boulders, noise and vibrations affecting the adjacent lands and structures.
During the drilling stage, the boreholes most likely won’t follow its planned straight trajectory, resulting in deviations to the trajectory being quite common. These increase with the depth of the boreholes and are caused by innumerous factors. It also should be taken into consideration the fact that benches almost never display a uniform behavior as is thought of in theory which makes it difficult to measure the real burden between the boreholes and the free face.
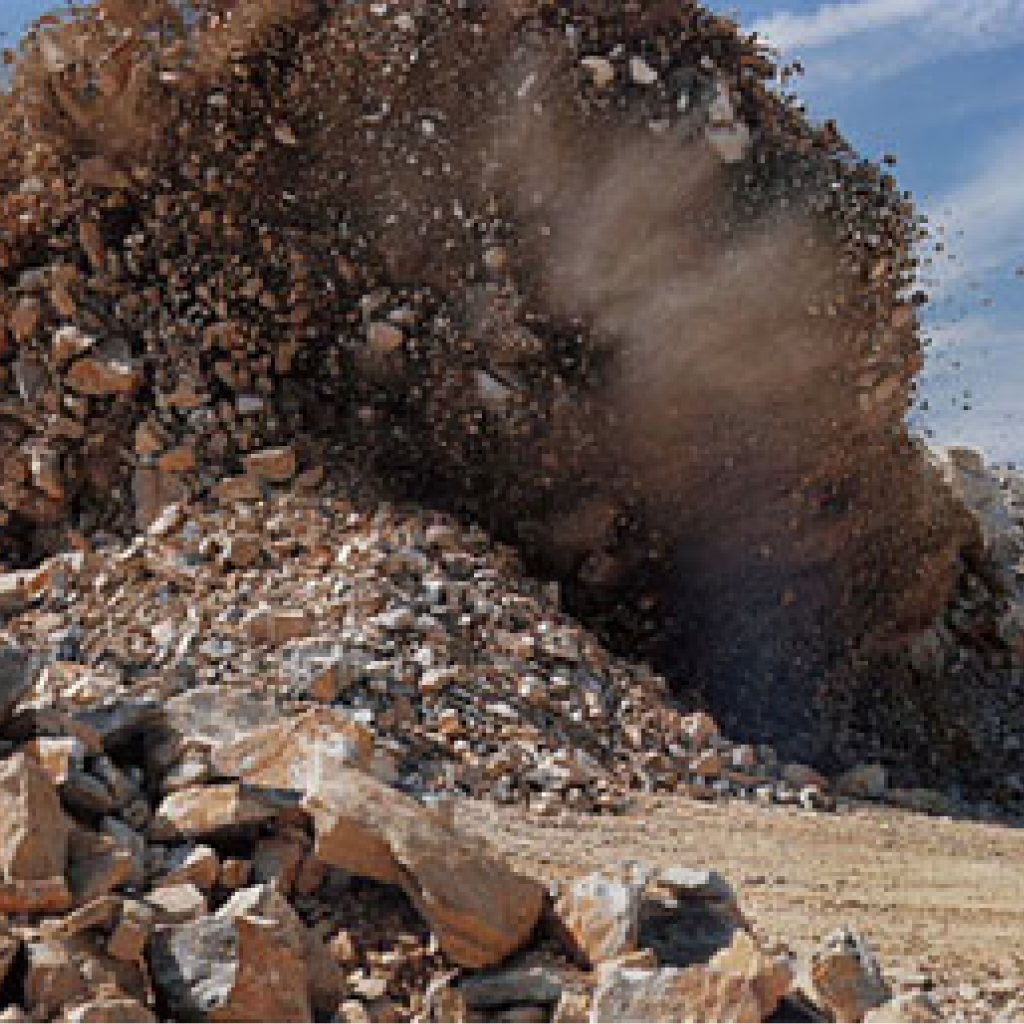
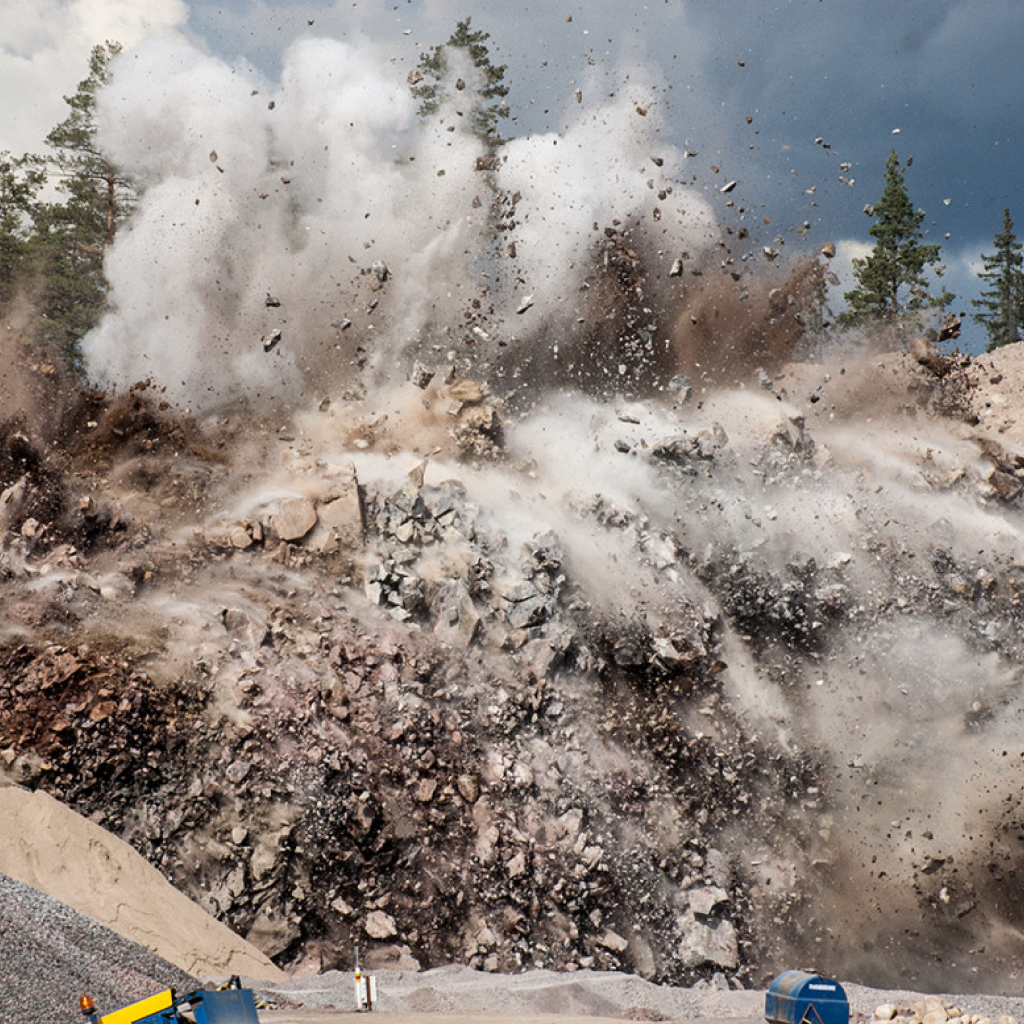
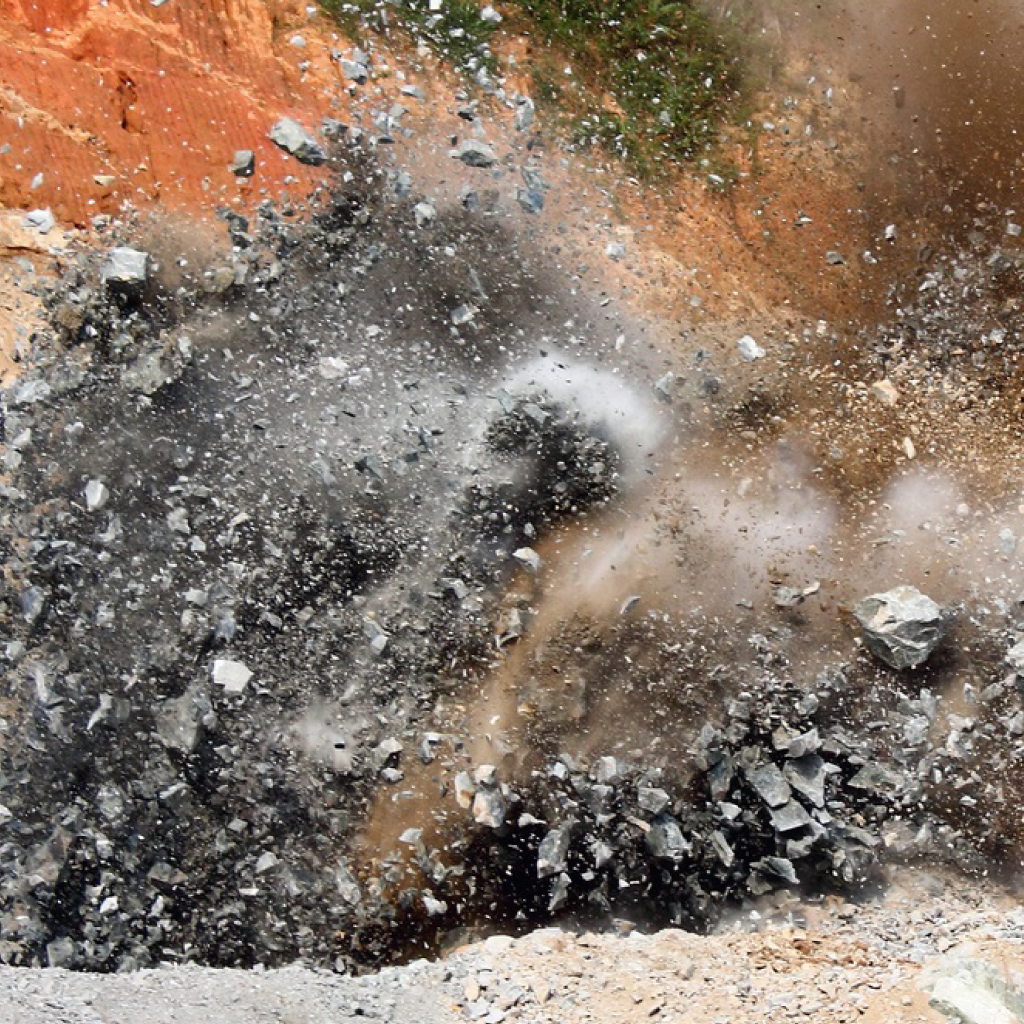
All of this compromises the correct distribution of explosive within the intended blasting area and can lead to fly rock*, noise, seismic waves, formation of fines or boulders with dimensions bigger than the ones that the crusher can act on, causing a decrease in safety and increasing the cost of exploration.
*Fly Rock is a phenomenon that consists of the projection of rock fragments beyond the quarry’s permitted work area, which represents a big danger for the population that inhabits close to the limit of said work area (SILVA, 1998).
A case study conducted in a quarry in the northern part of Portugal is presented below. Techniques of optimization to diminish the formation of boulders and fly rock were applied such as an inclinometer (for borehole deviation control), 3D modeling (using the O-Pitblast software), mapping of benches (with the use of drones) for study of free faces and positioning of remaining boreholes in relation to the first row.
Visual Inspection
In a preliminary stage, a visual inspection was conducted in the quarry and something that really stood out was the number of boulders.
Boulder formation is an issue that can be associated with several factors such as:
- Inadequate blast design parameters;
- Inefficient control of drilling stage;
- Geological conditions;
- Tie-up issues, etc…
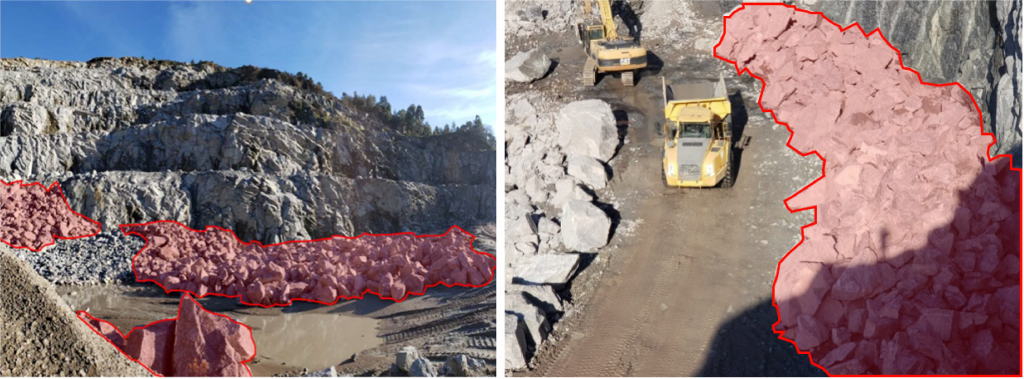
The ideal scenario would be to obtain the adequate granulometry in the entirety of the rock mass thus eliminating the need to perform a secondary blast and avoid spending extra monetary resources with the blast stage.
The optimization of the blast not only leads to the reduction of costs associated to the blasting operation but also to the remaining costs related to the drilling, loading, hauling and crushing stages. It is also not ideal for the formation of boulders to occur since it requires a secondary blast, an operational cost associated with this activity and may lead to the increase of risk of fly rock.
In that case, alternatives methods that provide more safety can be used such as hydraulic hammer, «drop ball», expansive cement, wedges, etc. All of these are associated with stages and consequently operational costs that can be minimized or even eliminated with an efficient blast.
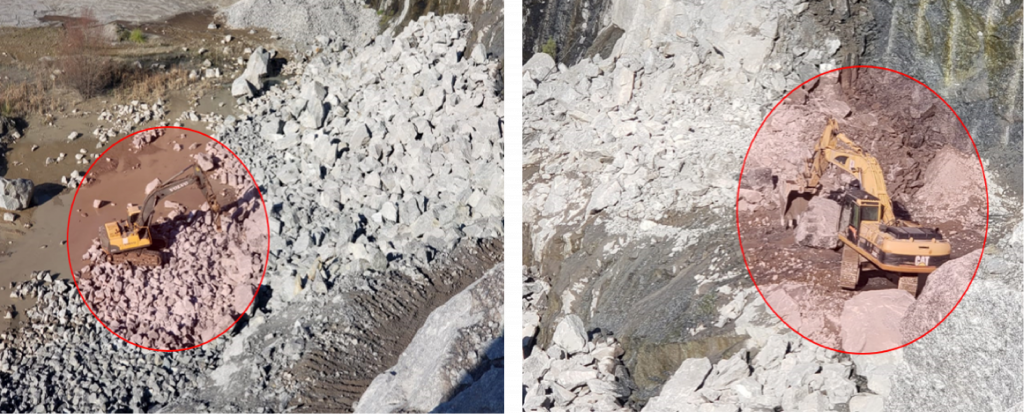
The fly rock ‘factor’ must always be taken into consideration since it can cause serious damages to not only personnel but to other people in adjacent communities, the company’s facilities, and nearby structures. The resulting consequences of this are breaks in production, corresponding fines and even the shutdown of the exploration altogether.
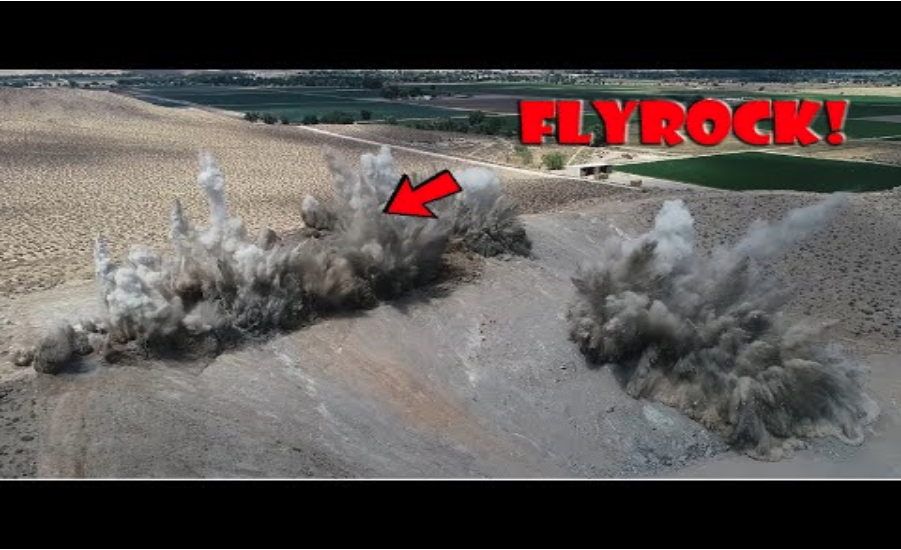
The aforementioned aspects can be better analysed and can be subject to improvements in terms of economy, safety and productivity by the optimization of the blast plan variables and with the use of technologies that facilitate the design of the blast plan. These take into consideration the geological conditions present in the quarry under analysis.
During the inspection works at the quarry, the drilling of the rock mass stood out since the boreholes seldom follow the intended trajectory, which in turn leads to them drifting apart from the original blast pattern. This gets worse as the depth of the boreholes increases.
In terms of fragmentation, the results must be compatible with the loading and hauling equipment as well as with the dimensions of the primary crusher, to avoid secondary blasting (LIMA, 2001).