Electronic detonators
Firing diagrams comprise the set of holes loaded with explosive with a given firing sequence. This is done with the use of detonators that serve to regulate the necessary delays between detonations of the charges (Bernardo, 2014).
An electronic detonator is protected by an electronic system because the ignition of the filament with an electric current only happens when the chip in the detonator gives information that the individual piece can fire (Bernardo, 2014).
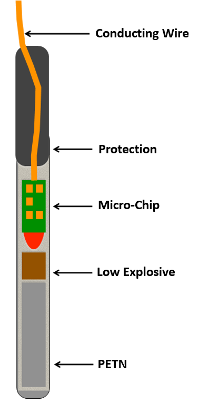
These are the best detonators on the market, in terms of usability, control and safety, suffering no consequences in the presence of disturbance currents. The system is protected with a chip that can only be triggered by a specific “Blast Box” that has received information from a specific “Logger”. In addition, it has the ability to allow disassembly up to a distance of 2 km, always allowing a safety distance for the responsible operator (Bernardo, 2014).
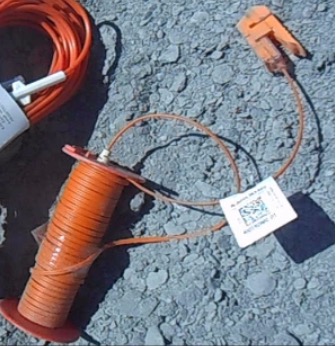
The electronic detonator has solved the problem of errors associated with the delay element, since the delay is now chip controlled. It also has no limitations on the number of delays per disassembly and has allowed the user not to be tied to the standard delays of 17ms, 25ms, 42ms or 67ms of the non-electric detonators. The user is thus able to choose any delay, down to 1ms intervals to avoid any problems with the frequency and amplitude of the vibrations (Bernardo, 2014).
Software like O-PitSurface provide the user with tools to plan and quickly design the timing set-up for electronic detonators. You can see the video below to see how this is done, in matter of minutes, allowing the user to make predictions and also export directly from the O-PitSurface to a “logger” machine.
Belly formations
The motion assisted by the detonation is not uniform throughout the length of the borehole. As can be seen from the figure 5. When the explosive detonates, the material is pushed in a manner that resembles a “belly”. This is due to the fact that the energy released by the explosive has the greatest influence in the central area. At the bottom of the hole, some of the energy of the explosive is counteracted by the frictional force exerted by the bench floor. At the top the amount of explosive is not only smaller due to the volume occupied by the blast, but also the material once fragmented is pulled by gravity to the central zone.
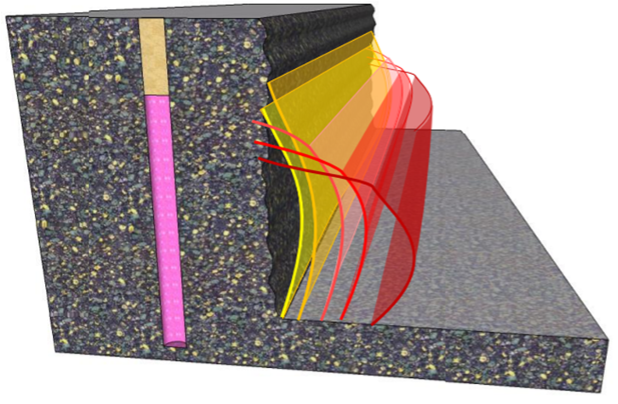
With the effect of belly creation in mind for the free front of the bench dismantling it can be established that the same principle can be applied for the entire dismantling. Basically, this belly formation is replicated until the blast reaches the back row.
This effect will then create bellies that in more technical terms can be called entrance membranes and exit membranes. To control the dilution problem, these membranes limit the zones of different contents. In the figure 6 you can see a representation of the shape change that the volume of material to be disassembled undergoes when it is displaced.
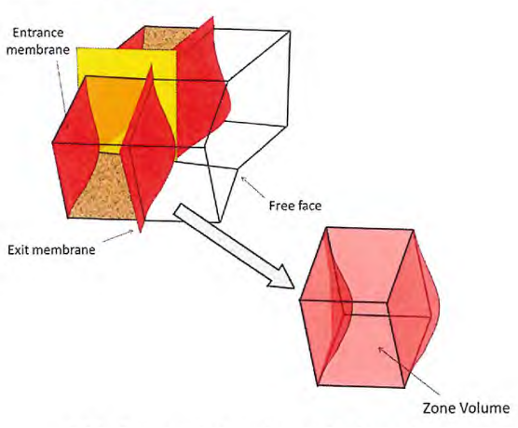
Blending
The importance of dilution control, especially in metal mining, is associated with the construction of mixtures to normalize the degree of entry of minerals in the treatment plant. In some cases, the content available after dismantling is varied, so its entry into the processing stage can be detrimental to production optimization (Domingo, Leite, Miranda, & Carrasco, 2015).
Since it is not feasible to change the regulation parameters of the processing operation, whenever the input material changes its content, it is necessary to have a technical mixing phase to stabilize the content of the material entering the processing plant.This process of controlled mixing of material of different grade content to regulate the input to the processing stage is called blending. The theory behind blending is that the disassembled material should be classified according to its content, density, volume and mass, as shown in table 1, allowing the person responsible for feeding the processing plant to make favorable blends with a view to achieving the optimum feed content.
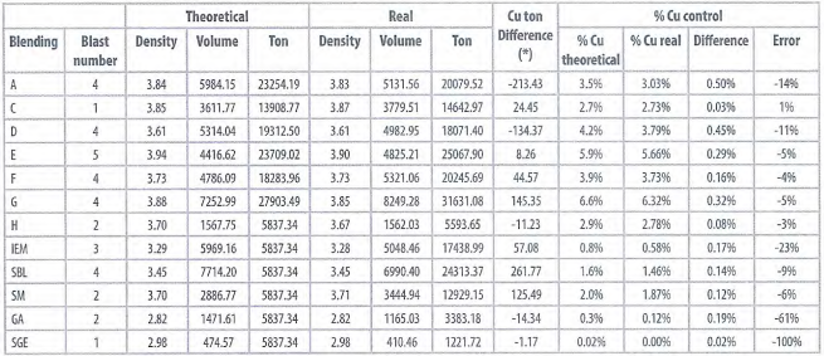
Final thoughts
Displacement of the disassembled material after detonation is a problem if it is not controlled, can reach high value losses, due to the loss of mineral grade.
The control of internal dilution starts with the correct and thorough classification of the material, while the control of external dilution is done during the blasting planning, minimizing the mixing of different material at the contacts between zones.
Depending on the objective of the mine, choked blast may be preferred, to negate movement, minimizing mixtures of material of different contents, or if the objective is to separate the material into piles of ore and waste material, then more complex timing, with electronic detonators, will be the most appropriate solution.
The monitoring and control of the blast movement for the material muckpiles segregation is important, not only for the minimization of the mineral dilution effect during the blast, but also to obtain different grade muckpiles in the case that some type of blending phase needs to happen.